6月の失敗鍛冶を念頭に置きながら、今回は気合いを入れ直し、焦らずゆっくり作業することにしました。最初は4日間の予定でしたが、何と倍も作業をしてしまいました。
6月から鋼は自分で購入しました。厚さ3mm 幅21cm 長さ1mの鋼の板を購入しました。2cm・2.5cm・3cmの幅で裁断してもらい、地金だけは工場の切れ端を頂き作業する事になりました。
今回の収穫は、四角い七輪の火床では、最初の段階の長さが12〜14cmが適当であることを確認したことです。
また。1,鋼材を何もしない状態 2,焼き入れ後何もしない 3,焼き入れ後空冷 4,焼き入れ後火床で焼き鈍しをする 5,焼き入れ後バーナーで焼き戻しをする。そして、それを同じ条件下でハンマーでたたく実験をしました。
1の何もしない状態の鋼はへの字に曲がりました。
2は一番もろく3つに折れました。
3・4・5は同じような折れ方ですが、やはり火床の脇でゆっくりと焼き戻しをした方が粘りがあるような感覚を持ちました。
上の結果から、自分の焼き鈍しの方法が充分ではなかった事を確認して、なまくらになる事をあまり恐れず加熱することが良いと言う結論に至りました。
今まで頂いていた鋼は粗研ぎの後、ドリルで穴が開けられたのですが、今回の鋼は、これ以上なまくらに出来ないと言う状態にしておいてもドリルで穴が開けられないほど硬いのです。同じ炭素工具鋼のSK材なのですが・・・・。 これ以上なまくらに出来ない状態でもこれだけ硬いのですから、焼き鈍しを充分にしても硬度が保てることを知りました。
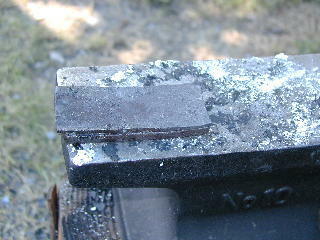
@ホウ砂をかけた状態 A軽く打ち合わせた状態の素材
ホウ砂は鍛接材、@の写真の右側ように、充分に加熱した鉄にまくとドローっと溶けだしますが、加熱が足りないと左の様に泡立ちます。熊公は溶けて全体に広がった方が作業しやすいです。今回は鉄粉を混ぜてみたり、混ぜないでホウ砂だけでやってみたりしましたが、変化はない様な気がしました。
Aの写真の時はハラハラします。上手く鋼と地金がくっつけよ!!と、祈る思いで作業をします。鍛冶作業の一番重要な部分だと思います。
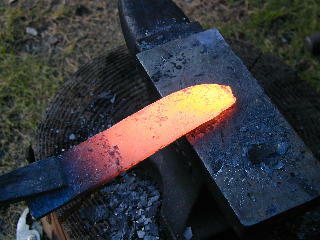
Bじっくりと鍛接の作業をして鋼と軟鉄が1枚の鉄の板になった状態 C切っ先部の成型
Bの状態になれば一安心。鍛接不足がないかを確認しながらまずは薄い直方体に仕上げます。今までの経験では、鍛接不足がある場合、地金が鋼の上に延びてくるような状態が起きます。これを見極めてしっかりと加熱し打ち付ける作業をしないと、必ず後で泣くことになります。
C・Dの作業は疲れますが楽しいです。自分のイメージする形に仕上げていくわけです。固い鉄が思い通りに形を変えていくのは本当に楽しいです。ただ、加熱しすぎにだけは気を遣います。
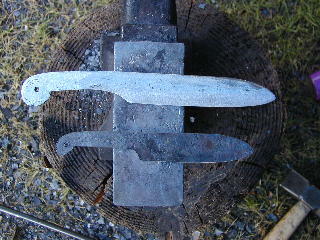
D柄部分の成型 E粗砥を終えた状態(上)
ハンドグラインダーを使い、形を整えます。Eの写真の下の方は火造りを終えた段階。最近は槌目がそろうようになってきました。その為、グラインダーがけが楽になりました。次回は「水打ち」と言う作業をするつもりです。
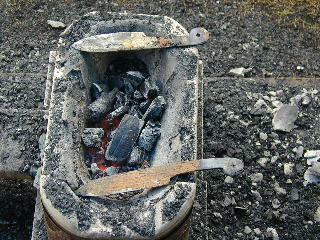
F焼刃土をぬった状態 G焼き鈍しの状況
Fの焼刃土ですが、伯父の家の前の畑に顔を出している粘土が実によいのです。焼き入れの際に炭の中で動かしても剥がれ落ちることがないのです。良いものを見つけました。教本の通り、この粘土に炭の粉と砥石の粉を混ぜて使っています。
Gの焼き鈍し、おそらく刃の部分の温度は200度くらいだと思います。炭が次第に小さくなるにつれて温度が下がってきますから、この方法が一番ベストなのではと、現在のところ考えています。
焼きぞりは、鋼側が延びるようにそります。地金で挟み込んだ物はあまり大きな焼きぞりは出ませんが、片側だけに鋼を付ける場合はスルメを火にかざしたようにグーンと曲がってきます。これを打ち戻すのにも、この焼き鈍しは欠かせません。ここまで作業して、最後に刃割れを起こして「ハイお終い!」では、あまりに悲しすぎます。今まで何度泣いたことでしょうか・・・・!!
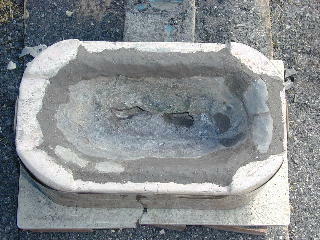
H1日使用した後の火床羽口付近は溶けています。 I毎回の修理状況。次の作業に備えます。
上の部分は毎回このようにかけてしまいます。
今回は柄部分を共金作りとしました。東北地方の古墳から出土する『蕨手刀』というものをイメージしてペティナイフを製作しました。長さ10cm・厚さ7mm(鋼3mm+地金4mm)・幅3cmの素材から全長22cm・刃部の最大幅約3cm・厚さ2mmのペティナイフが出来ました。
写真(E・F)の物は、大きい方が長さ12.5cm 小さい方が8cmの素材(幅・厚さは前述通り)から作りました。この材料の長さの違いで、大きい方が全長26cm、小さい方が全長20cmのペティナイフが仕上がりました。
仕上げる物の厚さ、素材の大きさ、打っていくときの疲労度など、色々な条件が考えられますが、薄刃にするのであれば2倍〜2.5倍の長さに仕上がることが分かりました。
粗研ぎを終えた写真の穴(E・F)は、熱いうちに鏨で開けた物です。これをガイドにして鋼用のドリルで穴あけをしましたがダメでした。結局はダイヤモンドヤスリを使って穴を成形することにしました。
今回の鍛冶作業では片刃のナイフを作るため、地金の片側に鋼を付ける作業を中心に行いました。7本を作りました。うち1本は21cmの素材を用いて作業してみたのですが、中央部に鍛接不足が起き、修正が効かず結局廃棄しましたので、6本出来たことになります。ただ、この6本のうちの1本は焼きぞりを戻す段階で刃割れを起こしました。これも完全な製品とは言えないですね・・・・。使った炭の総量は35kgです。こう考えると1本作るのに5kg位の炭を使うことになります。上手くなれば一度に平行して何本かの制作が出来るようになるのでしょうが、現在の熊公の技術では1本が精一杯です。
今回は6月の失敗鍛冶の経験を充分に活かせたものと思います。七輪の火床に丁度良い大きさの素材を見つけだせたことは今後の作業が前進するものと思われます。
(2002.08.18)
|